DOE strategies for zero energy construction
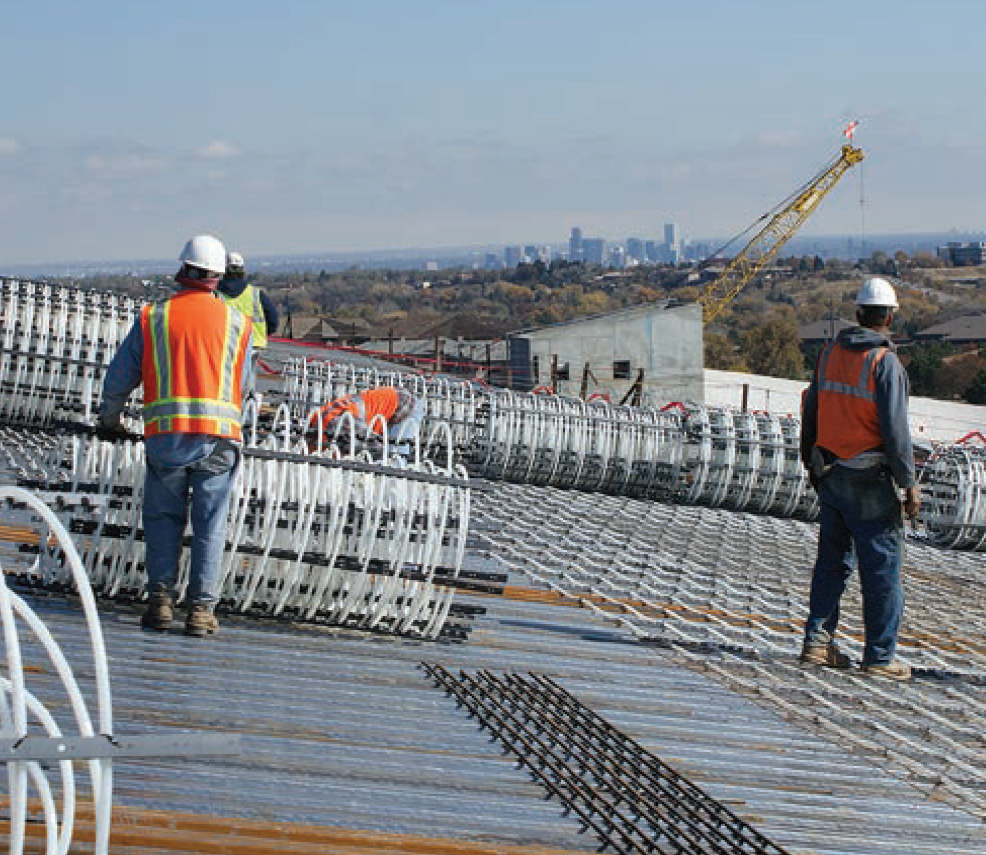
High-Performance Design and Construction on a Budget
Momentum behind zero energy building design and construction is increasing, presenting a tremendous opportunity for advancing energy performance in the commercial building industry. At the same time, there is a lingering perception that zero energy buildings—which produce as much renewable energy as the total energy they consume on an annual basis—must be cost prohibitive or limited to showcase projects. Fortunately, an increasing number of projects are demonstrating that high performance can be achieved within typical budgets. This factsheet highlights replicable, recommended strategies for achieving high performance on a budget, based on experiences from past projects. When applied holistically, the recommended cost control strategies promote innovative design and construction solutions that can facilitate the achievement of a wide range of aggressive energy goals, whether zero energy or otherwise.
Overarching Principles
To get the most out of cost control opportunities, the recommended strategies should be implemented with the following overarching principles in mind:
• Select a delivery method that elevates the importance of energy performance to be on par with other project objectives.
Including energy efficiency as a minimum requirement in a competitive delivery process promotes the innovation in the design and construction industry that is necessary to meet an owner’s goal of high performance on a budget.
• Emphasize integrated design and team communication.
Integrated design results in design and construction solutions that cost less and perform better. Making design and construction decisions as a team limits misunderstandings during construction and ensures that individual expertise is effectively utilized. This level of communication and collaboration is critical to leveraging integrated design principles and implementing cost control strategies.
• Leverage energy modeling early and often.
When design and construction options are being evaluated, energy modeling should be used to assess the energy performance implications of those options. Energy modeling throughout the project can help ensure that project decisions contribute to the achievement of energy performance goals.
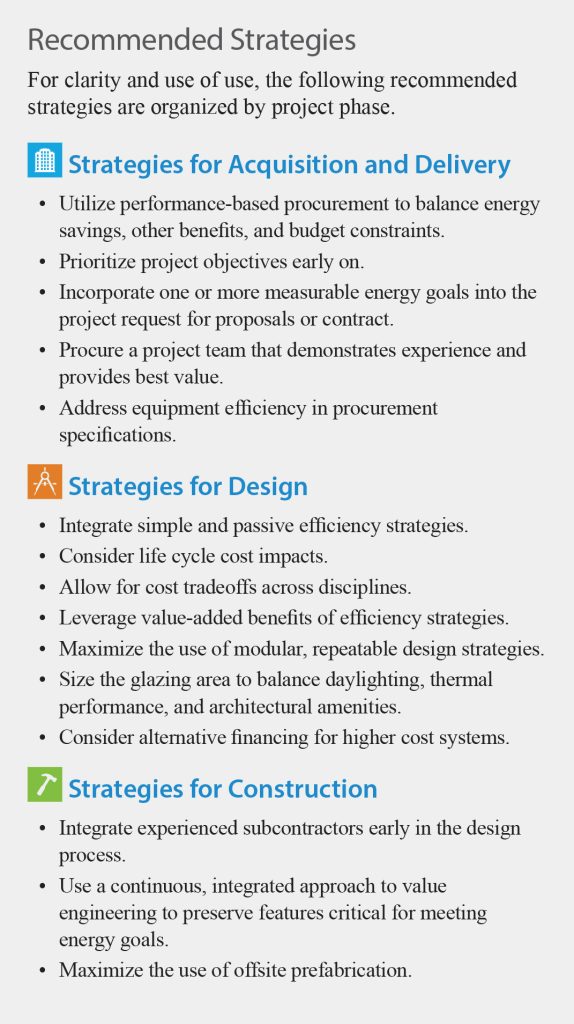
Industry Example
Allow for Cost Tradeoffs Across Disciplines
By considering construction process impacts, project teams can more effectively compare the first costs of construction alternatives during the design phase. A common mistake that project teams make when evaluating the first costs of competing design and construction strategies is to consider only material or equipment costs. In reality, installation costs can also differ significantly for different strategies. Exterior walls constructed with insulated concrete forms (ICFs) illustrate this concept well. Ken Seibert of CMTA observes from projects in Kentucky that:
• Traditional masonry construction has a lower material cost, but ICF walls can be constructed more quickly, reducing labor costs. ICF also enables streamlined scheduling of skilled trades work. With typical masonry construction, electrical and plumbing subcontractors need to be onsite throughout wall construction; with ICF, electrical and plumbing subcontractors do not need to be onsite until after the walls go up, further reducing labor costs.
• After accounting for streamlined construction, the cost of ICF becomes comparable to that for typical masonry construction. For these reasons, ICF has become a popular option for education, commercial office, healthcare, and hotel construction projects in Kentucky.
• Because of the speed of ICF construction, many projects also use ICF for interior masonry. As contractors gain experience with ICF construction, the cost of implementing ICF continues to decrease.
• There is an overall shortage of skilled masonry labor, and the availability of masonry subcontractors can often dictate construction schedules.
From an energy perspective, ICF is helpful because it provides a tight air barrier, which helps to reduce heating, ventilation, and air conditioning loads. Careful accounting of construction costs enables projects to leverage ICF and take advantage of the energy efficiency benefit.
NREL Campus Example
Maximize the Use of Offsite Prefabrication
Facing an extremely tight construction schedule, the contractor who installed the radiant heating and cooling tubing in NREL’s zero energy office building looked to prefabrication. Custom-designed, prepressurized, prefabricated rollout mats enabled the contractor to manufacture and test all 42 miles of radiant slab tubing in a controlled offsite environment. The tubing mats were customized to fit the design of the floor plan and its radiant heating and cooling zone network. Once the building’s decks were ready, the mats were simply crane-lifted into the appropriate place, rolled out, tied down, and connected to the larger network. The mats were installed in just 2 days, beating the aggressive 5-day construction deadline by a full 3 days. The contractor estimates that conventional radiant system installation techniques would have taken 60 days longer—far longer than allowed by the schedule.
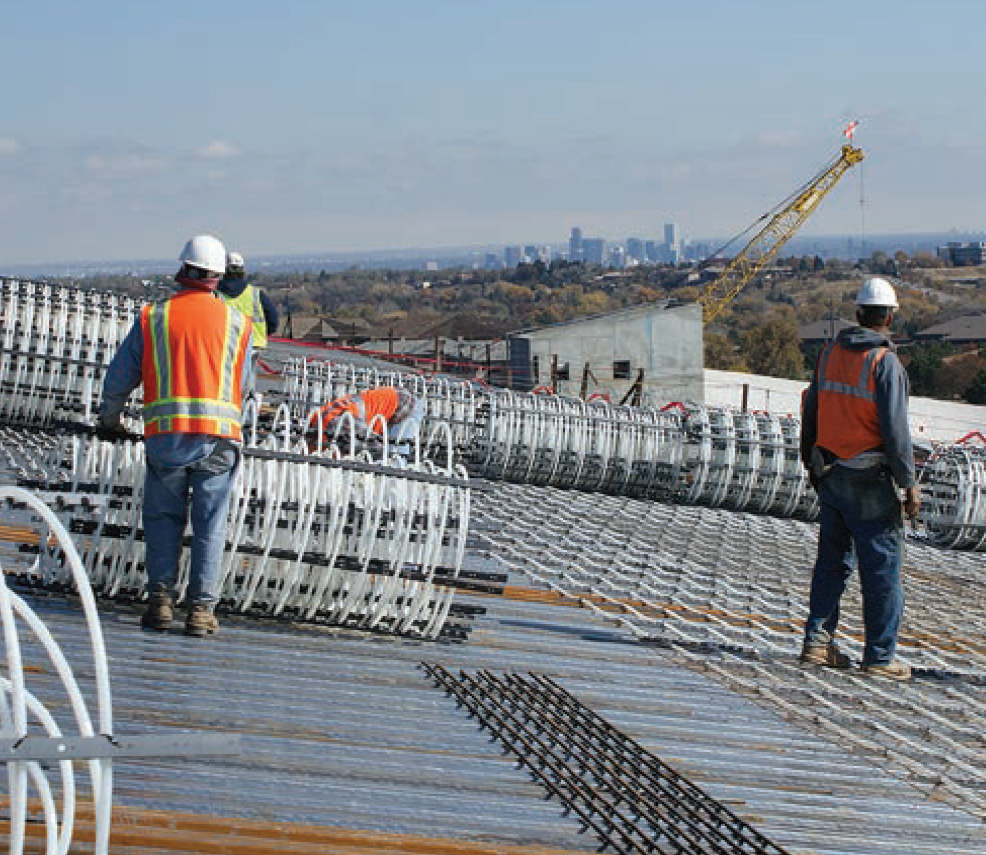
Original Story By:
National Renewable Energy Laboratory