Field of Dreams – Walton Passive House
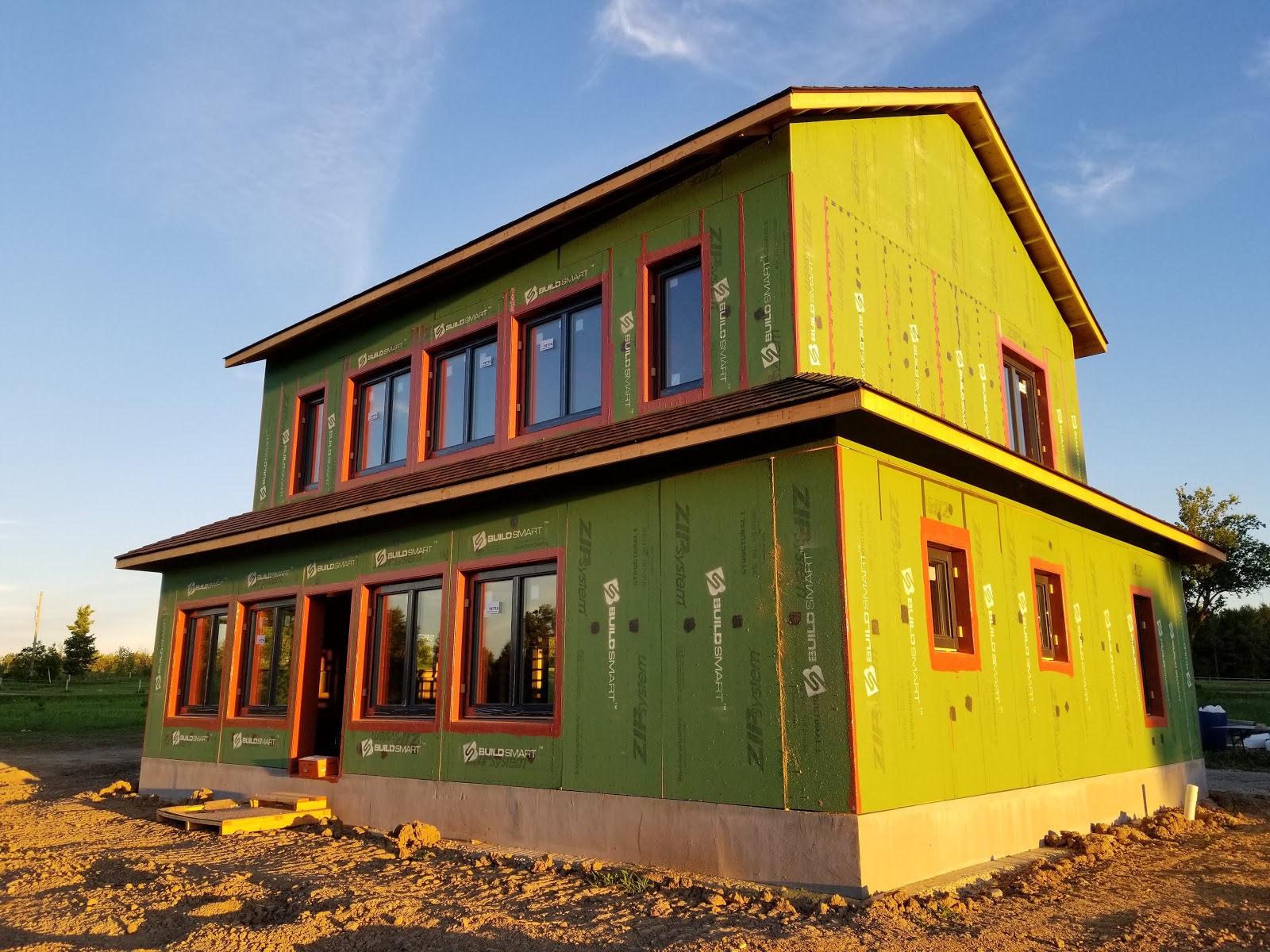
In the film Field of Dreams, farmer Ray Kinsella has a vision that compels him to build a baseball field in the middle of a corn patch. Chris Lee had a similar vision – to build a house in the middle of his corn field for himself and his wife, Judy. Several years ago, the Lee’s installed a 100kW solar array on their barn, so their carbon footprint was already small, but going further they decided to build an ultra-low energy Passive House. Prefabricated construction was chosen to reduce impacts to an adjacent, environmentally sensitive, wetland which Chris has restored over the past decade.
After some self-directed research, Chris found and hired Rob Blakeney who is providing Passive House consulting and engineering on the project. Through his firm Local Impact Design, Blakeney provides engineering services for high-performance buildings, including applied building science, energy modeling, mechanical HVAC, structural analysis, rooftop solar, and rainwater/greywater harvesting. Blakeney is convinced that Passive House is the most economical way to build. In regards to cost of ownership, by using a systemized design approach, and prefabrication, it can also be on par with traditional building capital cost.
|“ The philosophy that BuildSMART and I share is that Passive House and prefab doesn’t have to be complicated and it doesn’t have to be more expensive than traditional home construction. Build SMART passive house panels are cheap, robust, and easy to install. We believe that this will allow us to take Passive House construction to the next level and make Passive House accessible to a wide audience.” |
– Rob Blakeney, Local Impact Design
The Walton Passive House incorporates several sustainable products and features:
- Build Equinox Conditioning heat pump ERV (CERV)
- AMVIC Earthtube
- BuildSMART J-form monolithic slab
- Vetta Windows
- BuildSMART prefabricated wall panels
- Euroshield Rubber Roofing
Each one is detailed below:

The Conditioning ERV (CERV), is a multi-function air exchanger that uses a heat pump to regulate heating, cooling, ventilation, and humidity. The heat pump uses air flow to concentrate heat so it does not require an outdoor unit. The first CERVs in Ontario are currently being installed in two projects by Blakeney, including The Walton Passive House and a Passive House in Haliburton.
The CERV uses air pollution sensors to continually monitor carbon dioxide and volatile organic compounds (VOCs), and ventilates as required to maintain a fresh and healthy home. Since this home will only have two occupants for most of the year, a demand-control ventilation strategy will save energy by ventilating only when required.
To keep the ventilation air at a comfortable temperature during extreme cold events, the CERV uses an auxiliary 5kW electric duct post-heater which is controlled and operated by the CERV unit. Designed to work in conjunction with heat-pump water heater, the heat pump in combination with the post-heater is able to deliver 17,000 BTU/hr which is sufficient for smaller homes and passive houses. Because heating, cooling, and ventilation is combined into one compact unit, it is great for smaller buildings with limited space.
Earth Tube
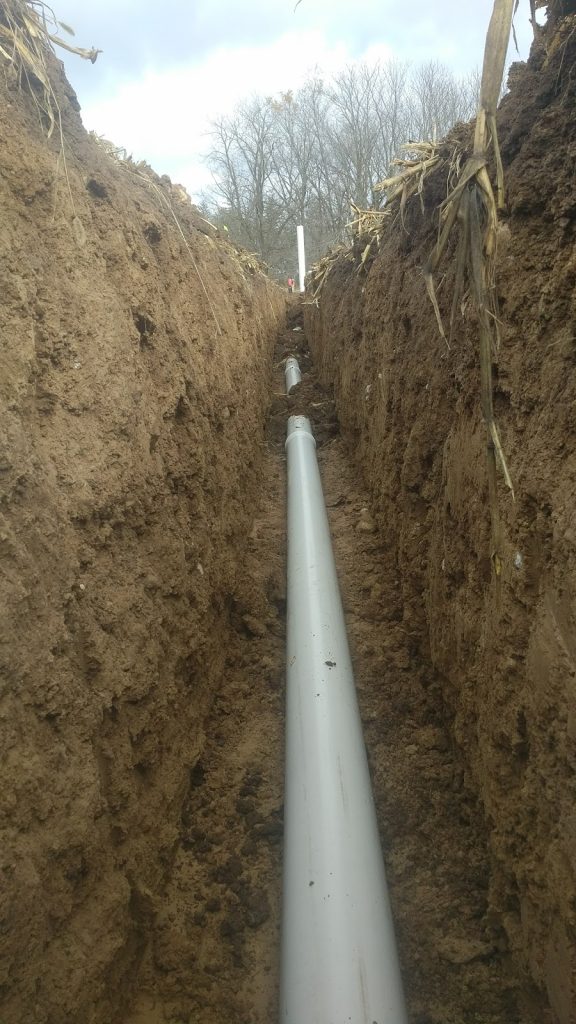
An earth tube is a passive design concept which works seamlessly with the CERV. In simple terms, it consists of buried pipe that draws fresh air through the ground to the home’s ventilator. Minimum depth should be about 6ft where ground temperature is pretty constant at 6-8C, providing up to 4,500 BTU/h of free pre-heating in the winter as well as pre-cooling and dehumidification in the summer and shoulder seasons. While thousands of residential earth tube systems have been installed in Europe, AMVIC is the only North American firm supplying a purpose-built earth tube package branded ECOAIR™. AMVIC’s “Residential Package” includes 180 ft of 8” PVC anti-microbial pipe and all necessary appurtenances including the prefab stainless steel inlet tower, filters, and condensate sump. Sloping the earth tube 1% toward a condensate sump prevents build-up of moisture (and mold growth). |
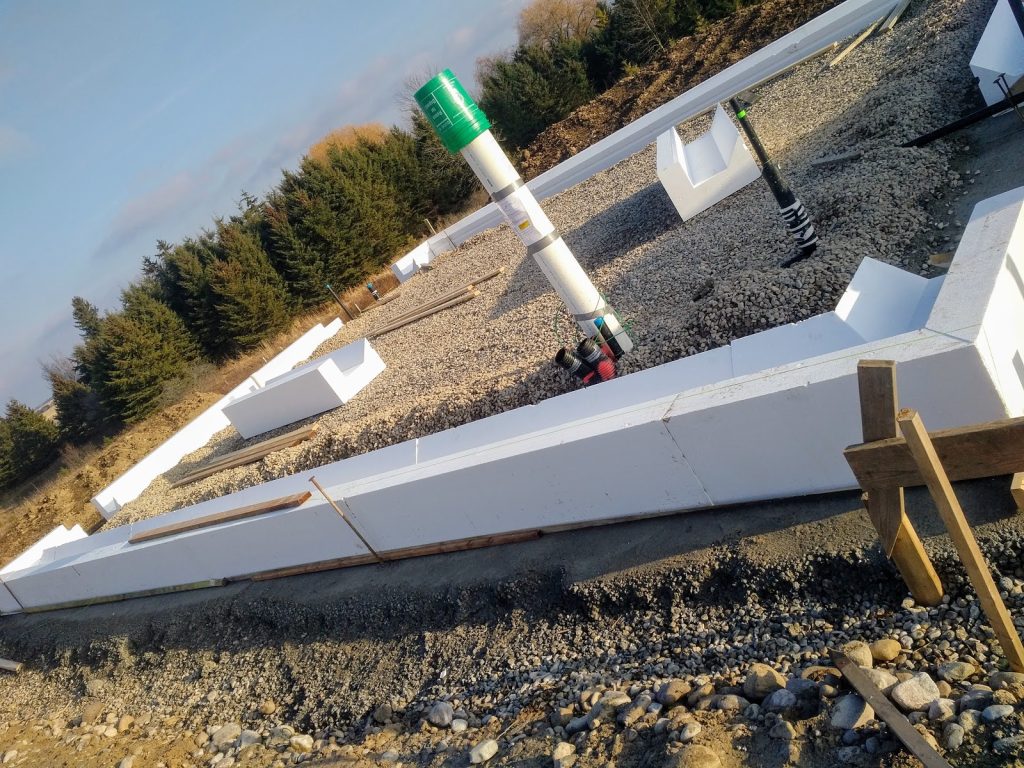
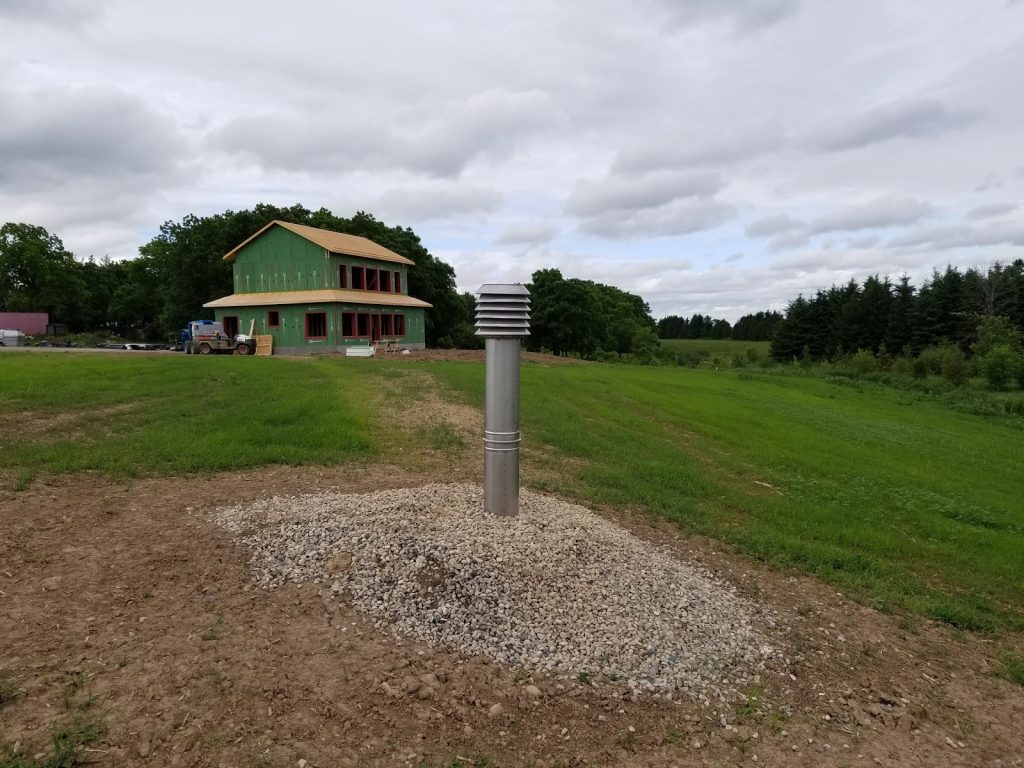
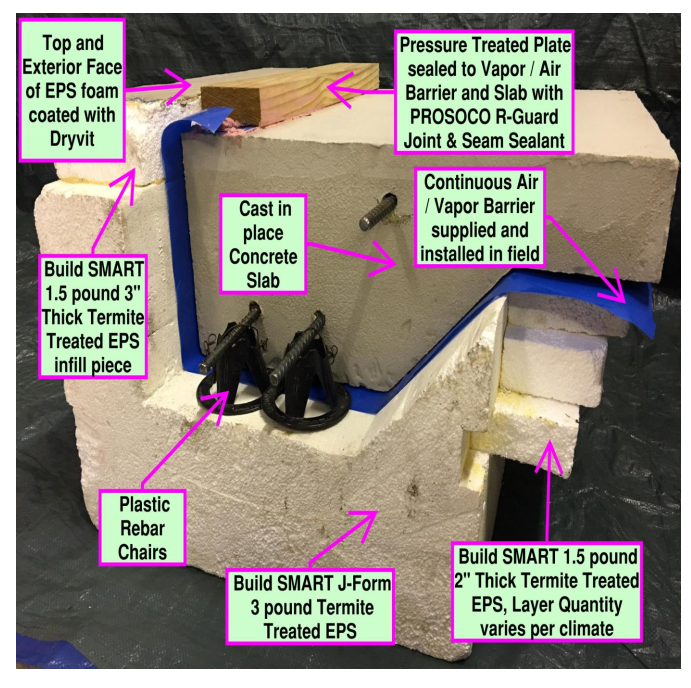
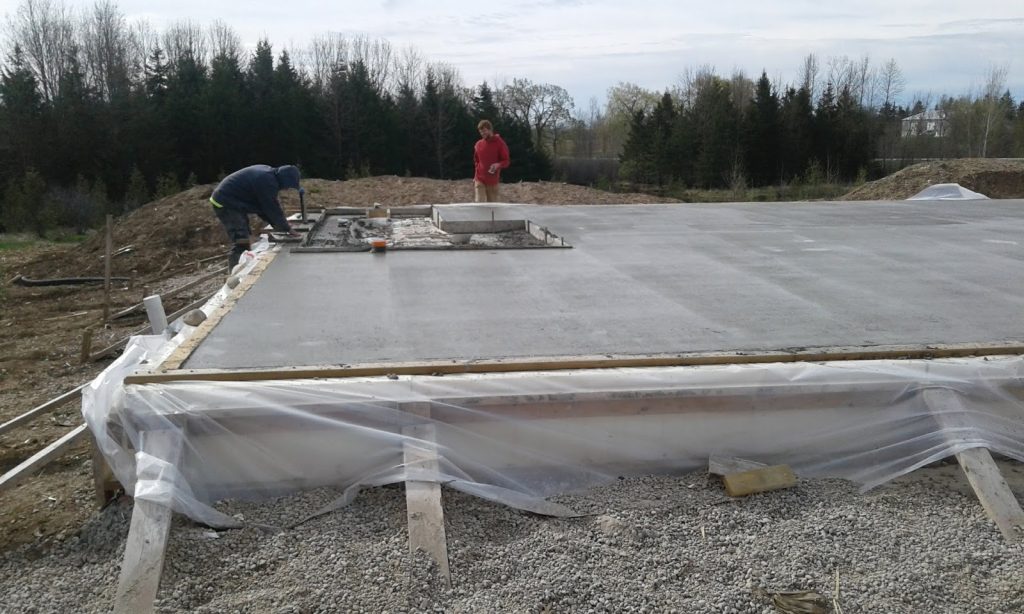
These slab foundation forms achieve high levels of energy performance with continuous insulation beneath the concrete slab and footing while eliminating multiple steps in the construction process. To isolate and insulate the foundation from ground contact, a high-density, termite-treated Build SMART J-form is installed in the footing excavation. This acts as the footing form and slab edge producing continuous insulation beneath the perimeter concrete footings and interior concrete slab. Cool!
Vetta Triple-Glazed Windows
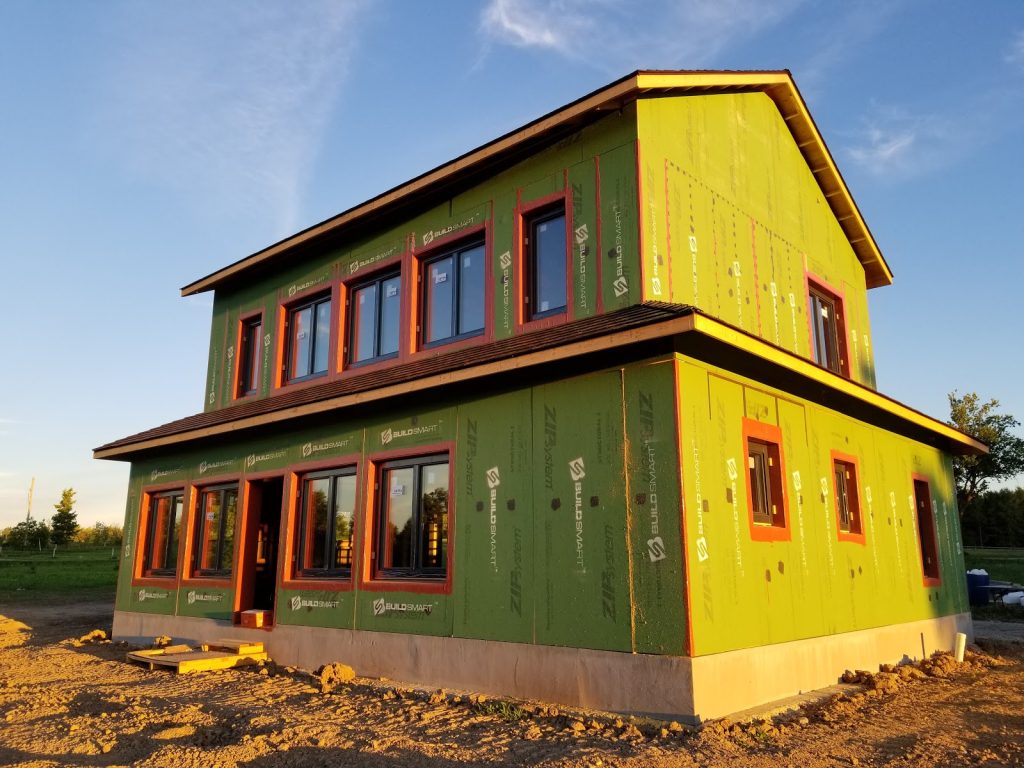
The Walton Passive House features ELITE 92 triple-glazed windows with passive house level performance verified by the International PassivHaus Institute. The Stratford-based supplier, Vetta Building Technologies Inc, owned by Alec Shalinsky and Sara James who have over 20 years of experience building homes | “We love these products that we are now bringing to Canada because we have first hand experience on how well they perform… With the environmental issues that the world is facing, we want to offer superior products to Canadians that will help them to achieve lower heating bills and much more comfort in their home while offering products that are hard to obtain in our country.” | – Shalinsky & James |
Build SMART Prefabricated Wall Panels
The Build SMART prefabricated panels used for the shell construction come with integral thermal, moisture, and air barriers, plus pre-installed Passive House certified, airtight triple glazed tilt & turn windows and doors. The wall has an interior stud wall utility chase, which makes wiring, plumbing, and finishing simple. Pre-engineered floor joists and roof trusses are supplied locally.
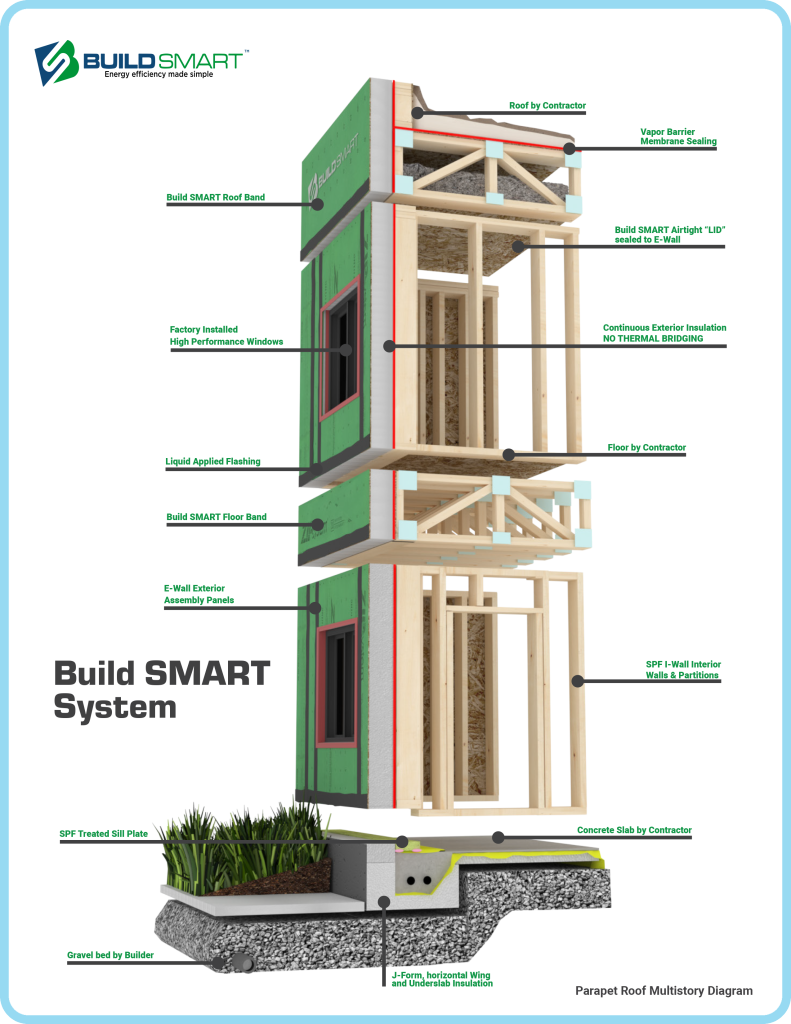
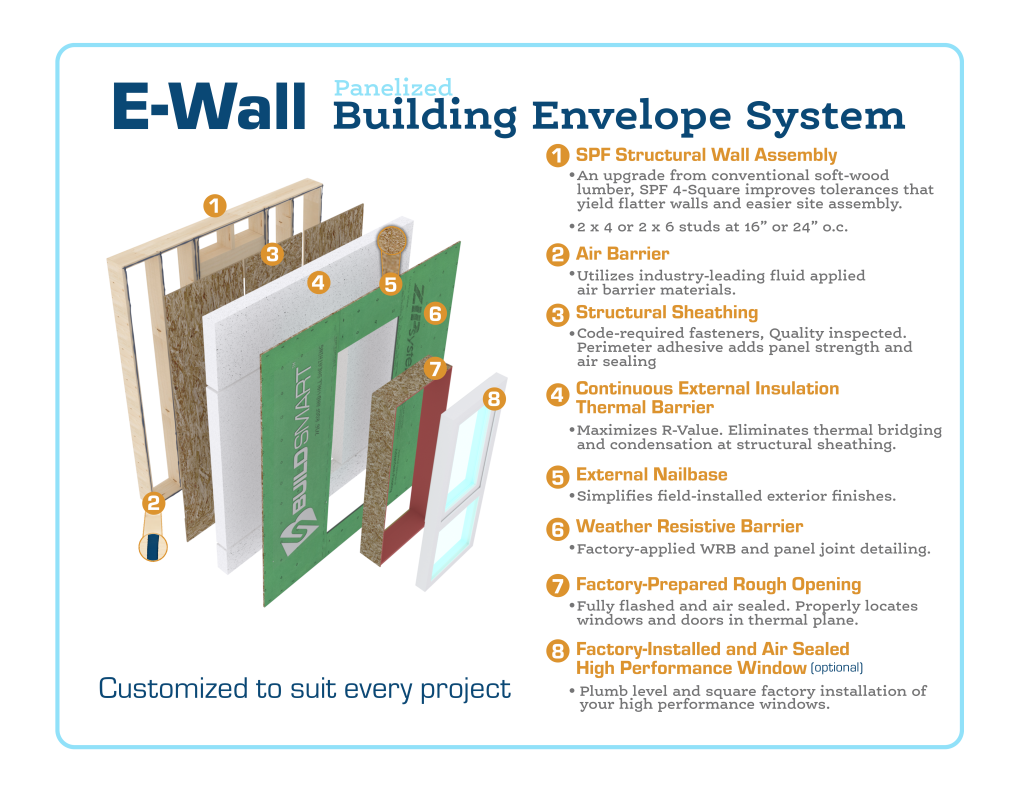
By standardizing components the design and pricing can be locked down early in the design phase. Installation is simple and can be measured in hours instead of weeks. The Walton project had a 3-framer crew that erected the entire first floor of a 2160 sqf house in a short six hours! The second floor also only took six hours, for a total of 264 linear ft of BuildSMART panels complete in 12 hours for a two-storey home. Builders Graham Borgdoff from Above Board Carpentry and Devon Henry from D J Henry Homes, are now convinced that this is the future of home building.
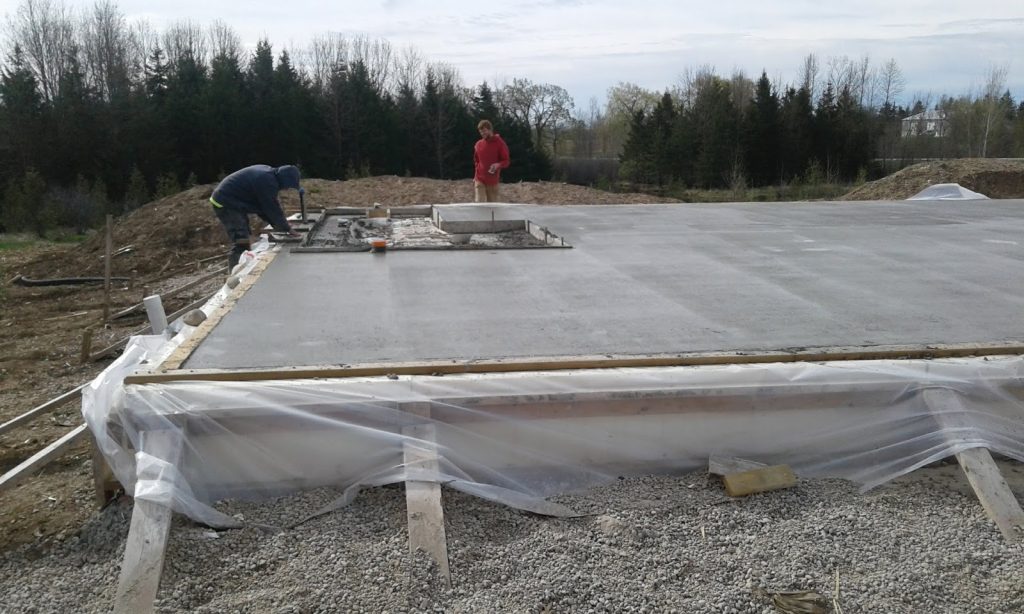
| “ I am super excited about the Build SMART pre-fab system. We were able to take the Lee project from foundation to shingle ready in 7 days. The on-site efficiency is incredible and helps us manage the timelines as weather becomes less of a factor. The Build Smart system advanced the technology of building science tremendously and brought the cost of high performance homes within the reach of common people. The fact is that conventional framing has been the way we have built homes for more than 100 years with little advancement to technology or process. Now is the time for change.” | – Graham Borgdorff, owner of Above Board Carpentry, builder for first two Build SMART projects in Ontario & Canada |
Traditional stick-built housing are at cost-parity with BuildSMART Passive house-quality prefabricated panels. BuildSMART is the first certified Passive House wall system in North America available and offers quality, flexibility, and low cost.
To speed up Installation, the team also commissioned floor panels from a local truss supplier. The panels arrived in six sections, complete with floor joists, beams and ply floor sheathing pre-assembled. The panels were lifted into place on the ground floor Build SMART walls using a HIAB four-wheel drive forklift. The first three panels were erected quickly with no issues, but the measurements of the remaining three panels were incorrect, requiring hours of re-work which negated any potential schedule and labour savings. Panelized floor panels, and even ganged roof trusses with roof sheathing pre-installed, promises to provide savings comparable to pre-fab walls, assuming that a higher degree of accuracy can be achieved.
| ” I often tell people that the Build SMART home can give people the performance of a Lamborghini with the affordability and mileage of a SMART car. ” | – Graham Borgdorff, owner of Above Board Carpentry |
Euroshield Rubber Roofing
Looks like cedar shakes but is not …. Beaumont Shake is the latest development from Euroshield Rubber Roofing from Calgary Alberta, officially launched in June, 2016. Euroshield® products contain 70% crumb rubber from tires and approximately 95% recycled content. The environmentally friendly choice in roofing, utilizing over 53% of the crumb rubber generated by Alberta crumb rubber processors to produce Euroshield® roofing.
Home Owners

As the Lee’s Field of Dreams vision becomes a reality, Chris and his wife Judy are very pleased thus far. As of mid-July, the house is at “lock-up” stage with shell and doors/windows installed; framing inspection passed; and awaits mechanical/electrical system installation. Recent blower door testing measured 0.51 air changes per hour at 50Pa (ACH50) – achieved on first try! This betters the Passive House threshold of 0.6ACH. Construction is targeted for completion in September 2018.
Putting all the pieces together, an air-tight thermal envelope with passive preconditioning via earth tube and active conditioning ERV, this home is set to outperform Passive House energy thresholds. This ultra-low energy Passive House using prefab construction will fit in nicely with the restored wetland within the corn field that they will soon call home.
| “An integrated, well-planned design/build process is essential and a key differentiator from a traditional stick built, code compliant home. Maintaining design integrity & budgets has demanded partners that understood our goals and contribute to them. We are fortunate in being able to say that our team members have each been a solid link in the chain of custody of the concept as our home is evolving from ideas to implementation and ultimately a whole new living experience.” | – Chris Lee |
Original Story By: Passive Buildings CA