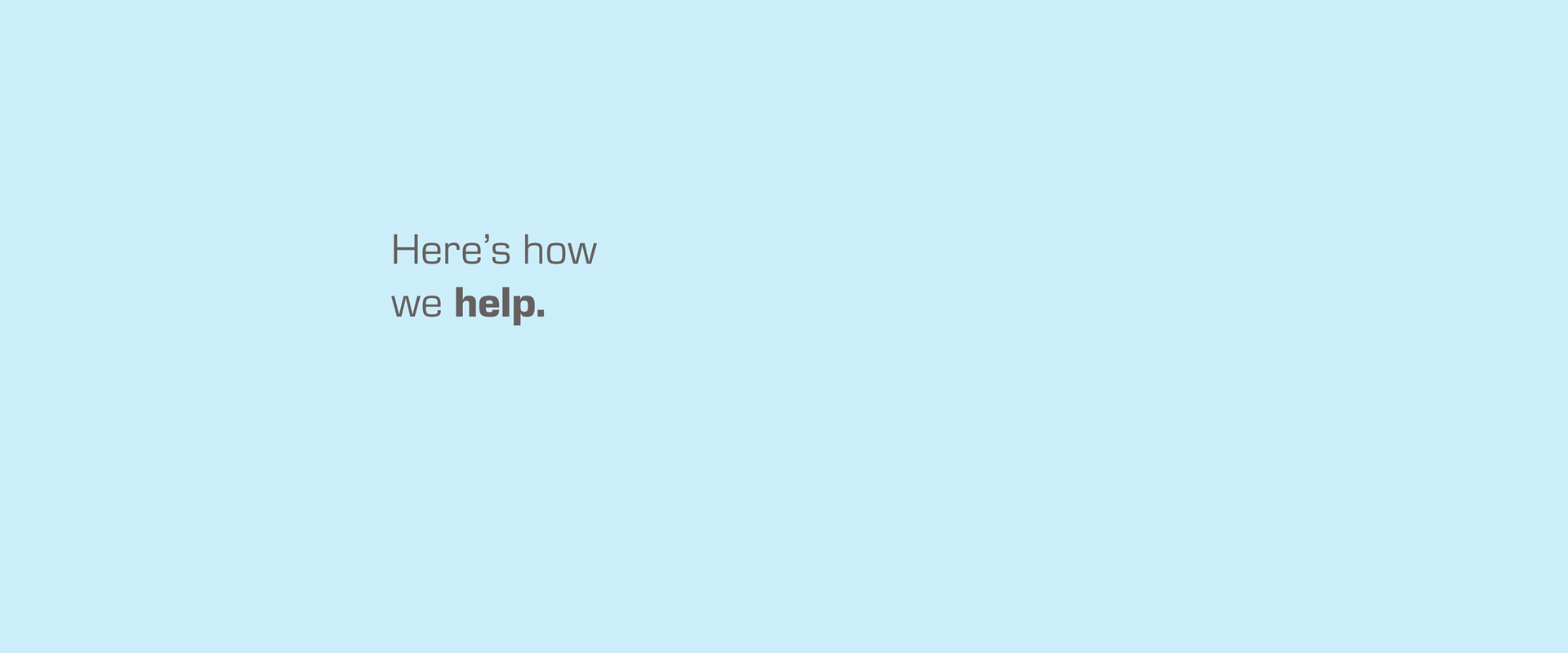
Got a quick question? It may have already been answered.
Check out our frequently asked questions section to see some of the most common inquiries into the revolutionary Build SMART prefabricated building envelope system process.
I’m reducing costs by specifying Build SMART J-forms for my insulated concrete slab-on-grade. What do I need to tell my concrete contractor?
We’re glad to hear that you're considering using Build SMART J-forms to reduce costs for your insulated concrete slab-on-grade. When discussing this with your contractor, it's important to provide clear instructions:
The Build SMART E-Wall System offers factory-built panels that have tighter tolerances compared to stick-built or on-site construction. This ensures effective air sealing and energy efficiency as the walls are constructed from the foundation to the roof.
To ensure the best results, it's crucial to use R-Guard Joint & Seam Filler or Build SMART Bond-N-Seal at all edges of the E-Wall System, including beneath the bottom plate. This will eliminate minor imperfections and optimize the system's performance. Additionally, it's essential to have a flat and level slab edge. Specify a floor flatness rating of FF 30 – 35 and a Floor Levelness rating of FL 20 – 25. Remember, higher numbers indicate better results.
If your contractor refers to a target "F" number instead, aim for F 30 or higher across the entire slab, including the edges. This will help prevent the slab edges from tapering down, which could necessitate the application of a thin layer of self-leveling grout before installing the treated bottom plate that supports the first level of the E-Wall System. By following these guidelines, you can avoid any potential delays in the installation of your complete E-Wall System.
By conveying these instructions to your concrete contractor, you'll ensure that your Build SMART J-forms are effectively implemented, resulting in cost savings and improved energy efficiency for your home.
For more detailed information on the J-Form system, we recommend downloading the Build SMART J-Form Diagram and the J-Form Foundation System Engineering Guide. These resources will provide you with comprehensive information and guidance on using the J-Form system in your project.
Why is Build SMART more expensive than conventional jobsite framing?
Build SMART may appear more expensive than conventional jobsite framing because it offers a comprehensive range of services beyond just framing. We collaborate closely with your design team to optimize both the cost and performance of your building. Our process involves vetting, sourcing, purchasing, receiving, and quality-inspecting all incoming materials used in your construction. This meticulous approach ensures that every component in your Build SMART system is carefully handled, stored securely indoors to prevent theft or damage from natural elements.
Furthermore, all building materials undergo machine-cutting to precise dimensions, resulting in tight dimensional tolerances and minimal material waste. To enhance structural integrity and building performance, nails and screw fasteners are supplemented with air sealing adhesives. You also have the option to include adhesive lamination for continuous exterior insulation, which eliminates thermal breaks that could compromise the building's performance and durability.
In the case of factory-installed windows, they are skillfully installed plumb, level, and square, and then fully air-sealed in their intended location. Once the proper window operation is confirmed, each panel is sequentially skidded for efficient transportation. Each skid is meticulously weather-protected, loaded, and securely secured, allowing for easy panel installation on-site.
While Build SMART may have a higher upfront cost, you can expect superior quality, reduced waste, enhanced energy efficiency, and improved building performance. Our comprehensive approach ensures that your project receives meticulous attention to detail at every stage, resulting in a high-quality, durable structure that meets your design requirements while optimizing long-term value.
How are rising material and labor costs impacting the cost of Build SMART Systems?
The rising costs of materials and labor have indeed had an impact on the overall cost of Build SMART Systems. However, we actively address these challenges to mitigate their impact on our clients.
When it comes to material costs, we maintain regular communication with our suppliers and leverage our purchasing power to seek the best possible prices. While it's challenging to predict and control fluctuations in lumber prices, we strive to reduce material costs wherever feasible.
In terms of labor, Build SMART takes a comprehensive approach. We provide all the necessary tools required for construction, eliminating the need for additional expenses on the part of the workers. Additionally, we offer enhanced worker benefits and predictable hours, which contribute to a more stable and motivated workforce. With these measures in place, we are able to pay lower hourly wages compared to what is typically seen in on-site construction.
One of the significant advantages of Build SMART Systems is the efficiency they bring to the construction process. By utilizing our pre-built panels and components, field assembly and dry-in time are substantially reduced. This streamlined approach helps to control higher labor costs typically associated with on-site construction.
While rising material and labor costs pose challenges, Build SMART actively addresses them through strategic purchasing, comprehensive worker support, and efficient construction practices. Our goal is to provide cost-effective solutions while maintaining the highest standards of quality and performance for our clients.
My Build SMART quote came back higher than I expected. Why so high?
The quote for your Build SMART project may appear higher than expected when compared to quotes for conventional on-site construction. However, it's crucial to consider the significant benefits and savings that come with choosing Build SMART. Here are some key factors to keep in mind:
Project Management Time: With Build SMART, you save valuable time and effort that would otherwise be spent on tasks such as vetting and sourcing building materials, laborers, and framers. You won't have to oversee and inspect the work completed by the on-site workforce or deal with trades and costly delays caused by inclement weather or scheduling conflicts. Additionally, Build SMART takes care of offloading, storing, securing, and weather-protecting essential materials. We also coordinate the delivery of completed Build SMART systems, streamlining the logistical aspects of the project.
On-site Construction Time: Build SMART significantly reduces on-site construction time by completing various phases of the building project while the site is being prepared and the foundation is installed. This includes tasks like constructing structural framing, installing structural sheathing, air sealing the building envelope, installing continuous exterior insulation, and detailing the weather resistive barrier within each E-Wall panel. If you opt for customer-selected windows, Build SMART takes care of sourcing, off-loading, quality inspecting, and securely storing high-performance windows before factory-installing them. This approach eliminates the need for additional time spent managing and disposing of construction waste. Furthermore, Build SMART's efficient process minimizes delays caused by unfavorable weather conditions or scheduling conflicts with trades.
Build SMART E-Wall Installation: Once Build SMART E-Wall systems arrive, a three-person crew can efficiently install the completed building envelope at an impressive rate of 35-40+ lineal feet per hour. This accelerated installation process substantially reduces dry-in time, minimizing the risk of further delays and property damage.
While the initial cost of a Build SMART project may be higher, the time, money, and frustration saved throughout the construction process can outweigh the upfront expenses. Build SMART's streamlined approach and efficient installation significantly shorten the overall construction timeline, ensuring a faster completion of your project.
By choosing Build SMART, you experience the benefits of reduced project management time, accelerated construction, and enhanced protection for your property.
Project Management Time
Vetting and sourcing essential building materials, laborers and framers.
Overseeing and inspecting work completed by site workforce.
Dealing with trades and costly jobsite delays caused by inclement weather or scheduling conflicts.
Offloading, storing, securing and weather-protecting essential materials.
Coordinating completed Build SMART systems delivery.
On-site Construction Time
Constructing Structural framing
Installing Structural sheathing
Air Sealing the Building Envelope Walls and Rough Openings
Installing Continuous Exterior Insulation
Detailing the Weather Resistive Barrier within each E-Wall panel
Sourcing customer selected windows (optional)
Off-loading, quality inspecting and securely storing high performance windows (optional)
Factory Installing high performance windows (optional)
Managing and disposing of waste generated from the above steps
Eliminating days-missed due to weather or trades scheduling conflicts
How can I control my costs without compromising building performance?
Controlling costs while maintaining building performance is a priority for any construction project. Here are two key strategies to achieve this:
- Simplify the Design: Complex projects tend to be more expensive as they require more materials, labor, and generate more waste. By opting for a simpler design, you can reduce costs without compromising building performance. Streamlining the design and focusing on essential features can help minimize material usage and labor requirements, resulting in cost savings.
- Minimize Design Changes: Thoroughly consider and plan how your home or commercial building will be used before starting construction. Avoiding design changes during the construction process is crucial to controlling costs. Change orders can lead to delays, additional expenses, and disruptions in the construction timeline. By carefully thinking through the design and ensuring it meets your requirements upfront, you can prevent costly modifications later on.
Why do I need continuous external insulation (CEI)?
Continuous external insulation (CEI) is essential for improving the energy efficiency and thermal performance of a building. Here's why it is necessary:
The resistance to heat transfer, or R-value, of a building material is determined by the amount of air or gas trapped within it. Kiln-dried softwood lumber, commonly used in structural framing, has an effective R-value of just over R-1 per inch due to the air trapped in its cells. On the other hand, fibrous insulations commonly used in stud bays have higher effective R-values, typically around R 3.5 or more per inch.
In walls that rely solely on stud bay insulation, the lower R-value of the structural framing creates interruptions in the continuity of the insulation layer. These interruptions, known as thermal bridges, occur continuously from the interior conditioned spaces to the building exterior. In a wood stud wall framed 16 inches on center, approximately 25-30% of the wall acts as a thermal bridge, allowing heat to escape from the building. This results in a reduction of the overall insulative value by 15-20%.
By installing continuous exterior insulation (CEI) over the sheathing and studs, the thermal bridging effect is minimized or eliminated. CEI creates a continuous layer of insulation that covers the entire exterior surface of the building, including the structural framing. This helps to significantly improve the efficiency of the thermal barrier by reducing heat transfer through thermal bridging.
By incorporating CEI into your building's design, you can enhance the overall energy efficiency, reduce heat loss, and create a more comfortable and sustainable indoor environment. CEI helps to create a continuous insulation layer without interruptions, improving the effectiveness of the insulation system and reducing energy consumption.
How do I convince my Client that wood frame and Build SMART are appropriate for my project?
How do you make the case?
How do you make the case?
When making the case for wood frame construction and Build SMART to your client, it's important to address their concerns and highlight the unique advantages of this approach. Here are some key points to consider:
- Addressing Perceptions: Acknowledge that some people may view wood frame construction as inferior due to misconceptions or limited awareness. Explain that while architects may not always consider wood frame above a certain height, the International Building Code (IBC) allows for wood frame construction up to six stories. Emphasize that wood frame construction, when done with proper building science principles, can provide excellent, high-quality, and durable buildings.
- Building Science Expertise: Highlight that Build SMART has fully embedded best practices and has vetted the material compatibilities of its wall panel assembly. Years of refining quality assurance and quality control processes ensure that the wall assembly is carefully detailed to prevent moisture, mold, and rot issues. This level of attention to detail and expertise cannot be replicated in traditional stick-built approaches.
- Affordability and Code Compliance: Emphasize that Build SMART offers a significant advantage by making it affordable to meet building code requirements and even achieve demanding standards like Passive House without requiring special skills, tools, or specialized builder knowledge. This affordability is derived from the cost-effectiveness of wood frame construction and the ability to achieve high performance through the engineered panelized system.
- Advantages of Wood Frame: Highlight the inherent advantages of wood frame construction, such as cost-effectiveness due to a large pool of competitive bidders, quick construction timelines, and sustainability. Wood is a North American-sourced material with low embodied energy and high embodied carbon. Additionally, wood frame structures are easy to deconstruct and reuse, contributing to a more sustainable building lifecycle.
- Advantages of the Manufactured Approach: Explain that the manufactured approach of Build SMART offers superior quality achieved in a controlled factory setting. This approach allows for fast-track production, starting while the team is still obtaining permit approval, preparing the site, and pouring the foundation. The faster assembly on-site ensures that the building is dried-in and ready for other trades to start work sooner, accelerating the overall construction timeline.
Describe your pre-construction services. Do you charge a fee?
Build SMART offers pre-construction services free of charge to support the design team and optimize the project. The services provided during various phases of the project include:
- SD Phase:During the Schematic Design (SD) phase, Build SMART can provide valuable input on factors such as building orientation, window-to-wall ratios, volume-to-skin ratios, and the continuity of the building envelope. Additionally, Build SMART can offer insights on the ease of prefabrication.
- DD Phase:In the Design Development (DD) phase, Build SMART can help optimize the energy and cost budgets of the project. By leveraging their expertise, we can provide suggestions and recommendations to enhance the overall efficiency and cost-effectiveness of the design.
- CD Phase:During the Construction Documents (CD) phase, Build SMART can provide model specification sections for specific systems like the J-Form and Underslab Insulation System, as well as the Wall panel system. These model spec sections serve as guidelines for the construction team, ensuring that the specified Build SMART components are incorporated correctly.
- Construction Phase:Throughout the construction phase, Build SMART offers shop drawings for approval before fabrication begins. These drawings detail the specifications and dimensions of the prefabricated components. Build SMART also provides pre-installation instructions to guide the contractor during the installation process. The prefabricated panels are then delivered to the job site for construction.
Can Build SMART help with cost estimating, coordination with the General Contractor, support with Architectural details, constructability and feasibility?
Budgeting and Pricing: Early in the design phase, for project budgeting purposes, we provide preliminary cost estimating for Build SMART’s exterior envelope components. We have a spreadsheet that allows comparison of our system with stick building or any kind of panelized system. We can run comparisons and or coach project members on using the spreadsheet themselves. When final bid documents are ready, Build SMART provides final pricing of our systems.
Construction Coordination: We work very closely with the GC. The panels are very easy to install, however, we want to maintain and build on our excellent reputation, so we go out of our way to help. We can adjust our production to match the GC’s sequencing, phasing and delivery needs.
Architectural Support: We make it easy for architects to work with our system. We also can involve air barrier and waterproofing experts free of charge from our sister company PROSOCO if there are any sealing challenges that go beyond the use of our panels. Generally, Build SMART has no impact on the A/E’s Construction Drawings and Specs. Floor Plans: Just show the wall thickness as agreed for the Build SMART wall panels. Provide outside dimensions and dimensions of the main door opening and any full height columns at the double height wall (the Contractor generally provides columns). Show any point load locations that may be required per your Structural Engineer (we can provide multiple studs in our panels for these locations.
Elevations: Build SMART panels can accommodate any Contractor provided exterior cladding and trim that you want. Sections: Just provide section cuts at the primary conditions, with vertical dimensions. Window Schedule or notes on the elevations provide sizes, operation types, etc. Specify windows in the normal way.
Support with constructability and feasibility: We recognize that Build SMART’s ultimate role is to provide a product – the building enclosure system - but our preference is to be considered part of the design and construction team. We believe the AIA Integrated Product Delivery report should serve as a road-map for interaction among project team members even where the contractual relationships are of the conventional type. The report states, “It should also be noted that a standard Design Bid Build project, or any project for that matter, would benefit from developing a strong team following bid acceptance. Byproducts of a strong team are a greater commitment to the project, improved communications and a willingness to work through disputes rather than resorting to an adversarial mentality. Although a traditional DBB project cannot be integrated, it can still benefit from the principles of integration.”
How has Build SMART's proprietary system been addressed on previous projects?
We assume here you mean the preparation of RFPs and specs for prospective bidders who would stick-build the same assembly or offer a competing panelized system. Architects have based their specs on the Build SMART model specification section, which allows for “comparable product by other manufacturers” in lieu of the basis of design Build SMART system. We can make it available for your use.
It is critical that my team, especially the General Contractor, understands exactly how Build SMART's panelized system reduces subcontractor costs and labor on site. What should I tell them?
The use of the E-Wall and J-Form slab insulation systems positively impact the project schedule by reducing project duration. Essentially, the Build SMART prefabricated systems are a fast-track strategy where building enclosure components are manufactured in our factory at the same time as the permit is being approved, the site clearing and foundation work is completed. When the foundation is cured and ready, the Build SMART panels show up sequentially numbered and arranged on the truck. The crew is building with panels instead of sticks so the building is dried in much faster. This is one of the big attractions to the Build SMART systems. Passive House air tightness is achieved in about half the normal time without special skills, tools or equipment.
Once installed, Build SMART E-Wall panels look very familiar to all the trades. They are looking at normal stud walls. They don’t even have to know that they are working on an extraordinarily high performance building. Therefore, with Build SMART, there is no premium cost for the unknowns that are often associated with SIP and other innovative structures.
Why should I use Build SMART? What’s in it for me?
Build SMART building envelope systems offer ultra-energy efficient construction while saving time and money for Contractors, Architects, Energy Modelers, Developers and Owners from day-1. We’ve streamlined adaptability and have eliminated no-value steps. Here’s how Build SMART benefits you:
For the Contractor, Build SMART systems provide the value-added building envelope components that are particularly demanding for a well-insulated and air-tight building. Commodity items like floor and roof trusses are readily sourced locally by the Contractor. With Build SMART, you build with prefab foundation insulation and exterior wall panels instead of sticks. Build SMART's wall panel system combines several construction steps in one and reduces or eliminates cranes, scaffolding and a whole lot of labor cost. Build SMART wall panel assemblies are familiar to every MEP subcontractor so NO premium cost for high-performance outcomes. Reduced stress for skilled labor because the enclosure building science is embedded in the panels (pre-installed windows, vapor controlled). No special skills, tools or equipment required.
For the designer, there’s no more guessing about assembly air tightness, thermal bridging or COST! By using Build SMART components, designers can create a high-performance building with the confidence and assurance of both quality and price. In addition, the Build SMART assemblies do not limit the design. Build SMART protects the design intent because every project is produced per order as YOU want it; as substrate for any aesthetic, from traditional to modern.
For the energy modeler, the Build SMART system offers modular R-values for climate-specific design. The meticulously modeled system uses the outside of the thermal envelope as the reference line, so increasing or decreasing the R-value of the components does not affect the initial modeled geometry - saving huge amounts of time in re-entering project geometry.
For the Owner, Build SMART gives you the low-energy, high-performance building you desire without limiting the style of your design. The Build SMART system can reduce your energy bills by 60-70%.
Can Build SMART work with an existing floor plan?
Yes! Give us a call or simply send your design documents and project requirements to us. If you are early in the design phase, we will respond with optimization ideas and preliminary budgeting. With developed design documents we can provide a quote.
How much customization is possible using the Build SMART system?
Every Build SMART project is custom - produced per order - so that your design intent is protected. Earlier in Build SMART's history we were limited to standard components, but now with computer driven production equipment we can cost-effectively accommodate a range of designs.
How long does it take to construct a Build SMART structure?
Our representatives will let you know the production backlog that we have already committed to. Of course, while Build SMART is producing wall panels, you will be busy getting the building permit, then preparing the site and pouring the foundation. When you are ready, the Build SMART truck will arrive with panels numbered and conveniently sequenced for fast and efficient construction. Builders tell us that a Build SMART project can be dried-in in half the time of conventional construction. That time reduction saves the related cost of labor and overhead.
How long will it take the components to ship once I place my order?
We schedule the production of wall panels to meet our commitments on each project. Leadtimes will vary.
What kinds of finishes – exterior and interior – are possible using Build SMART panels?
Build SMART wall panels accommodate interior finishes and exterior trim, siding as you have designed them.
What about my mechanical systems? How do they integrate into a Build SMART design?
Mechanical, electrical and plumbing systems are installed just like any other project. We recommend submitting your MEP Rough Opening Details which will help move things along faster. The Build SMART Installation Manual includes instructions for properly sealing penetrations through the exterior wall.
What other products or services are available from Build SMART?
Build SMART is a provider of high performance building enclosure systems. We do not aspire to be Contractors or Architects. We do not build and we do not design buildings. Instead we collaborate with and support our team partners. We highly value their support and advocacy for Build SMART.
Can I talk to a real person for more information?
Does Build SMART offer Architectural design services?
Build SMART does not offer architectural services. We do not make Construction drawings. Typically we produce shop drawings after an agreement has been signed. Generally, the Architect produces construction drawings.
Floor Plans: No impact due to Build SMART. Just show the wall thickness as agreed for the Build SMART wall panels. Provide outside dimensions and dimensions of the main door opening and any full height columns at the double height wall (the Contractor generally provides columns). Show any point load locations that may be required per your Structural Engineer (we can provide multiple studs in our panels for these locations).
Elevations: No impact due to Build SMART. Indicate any cladding and trim that you want. Sections: No impact due to Build SMART. Just show the double height section and the floor structure at the Mezz. Section. Provide vertical dimensions. Window Schedule or notes on the Elevations: No impact due to Build SMART. Provide sizes, manufacturer and model, operation types, etc. Build SMART shop drawings will include window details, so you don’t need to include them in the CD set. Just send project documents (SD, DD, or CD's) and we will freely collaborate with the design team.
How much insulation do I need where I’m building?
Proper building design today starts with a good energy analysis. Build SMART systems give the Engineer a high degree of confidence about the thermal enclosure. We generally exceeding the minimum IECC insulation requirements because high performance buildings - even Passive House performance - is proven to be a very good investment with a very short payback period.
I already have a builder. How can our builder work with Build SMART on our project?
We offer training for builders at construction kick-off so that crews work efficiently. Just provide us the contact information for your builder, and we’ll take it from there to meet your project’s needs at a cost you both can rely on.
How do I get started with Build SMART?
Call us as early as possible in your planning stage. Our representatives will be happy to freely assist you. We will help you optimize your energy and cost budgets. When you have drawings, send them across. It's that easy.
You say you can customize wall panels for each project, but I don’t see anything about choosing the type of lumber. Couldn’t I save money on my panel package if Build SMART used solid sawn lumber rather than LSL lumber?
It’s really a case of “pay me now or pay me later.”
In addition to accommodating a more precise fabrication process, high quality engineered lumber ensures long term durability and energy efficient performance of your completed Build SMART envelope.
Shrinkage of solid sawn lumber, caused as studs and wall plates dry and shrink down to equilibrium, can account for 1 inch of vertical shrinkage in a four-story wood framed building. Imagine what that does to the investment you’ve made in sealing out air and water leaks. What it does to the operation of high-performance windows and doors.
The critical point, for example, is where the interior wood frame might abut a concrete block stairwell. This condition requires careful detailing by the Architect. Build SMART has addressed the issue at exterior walls and virtually eliminated by the vertical shrinkage by using engineered lumber.
Build SMART employs advanced Laminated Strand Lumber (LSL) and Laminated Veneer Lumber (LVL) in all our assemblies to minimize building movement. LSL and LVL are engineered and manufactured at a moisture content that matches that of most fully enclosed and occupied structures (*FPL 2010) virtually eliminating shrinkage common to other structures.
Builders will appreciate the time savings realized during site erection of these more precisely fabricated panels. Owners will appreciate the uncompromising performance and reduced maintenance/repair costs over time. Occupants will appreciate the trouble free, leak free performance of the walls that surround them. Engineered lumber is clearly an excellent investment in improved quality.
Does Build SMART have a solution if I want to use precast basement instead of a slab-on-grade?
When Build SMART has a project in the Eastern third of the US that involves a basement rather than slab-on-grade, we recommend Ideal Building Systems (IBS) insulated foundation panels.
The Ideal precast basement panels have been shown to work well with our Build SMART panels. For above-ground walls that will be most familiar to contractors installing exterior and interior components to finish out a house, we believe the Build Smart panels are a better choice.