“Beautifully designed and beautifully built”
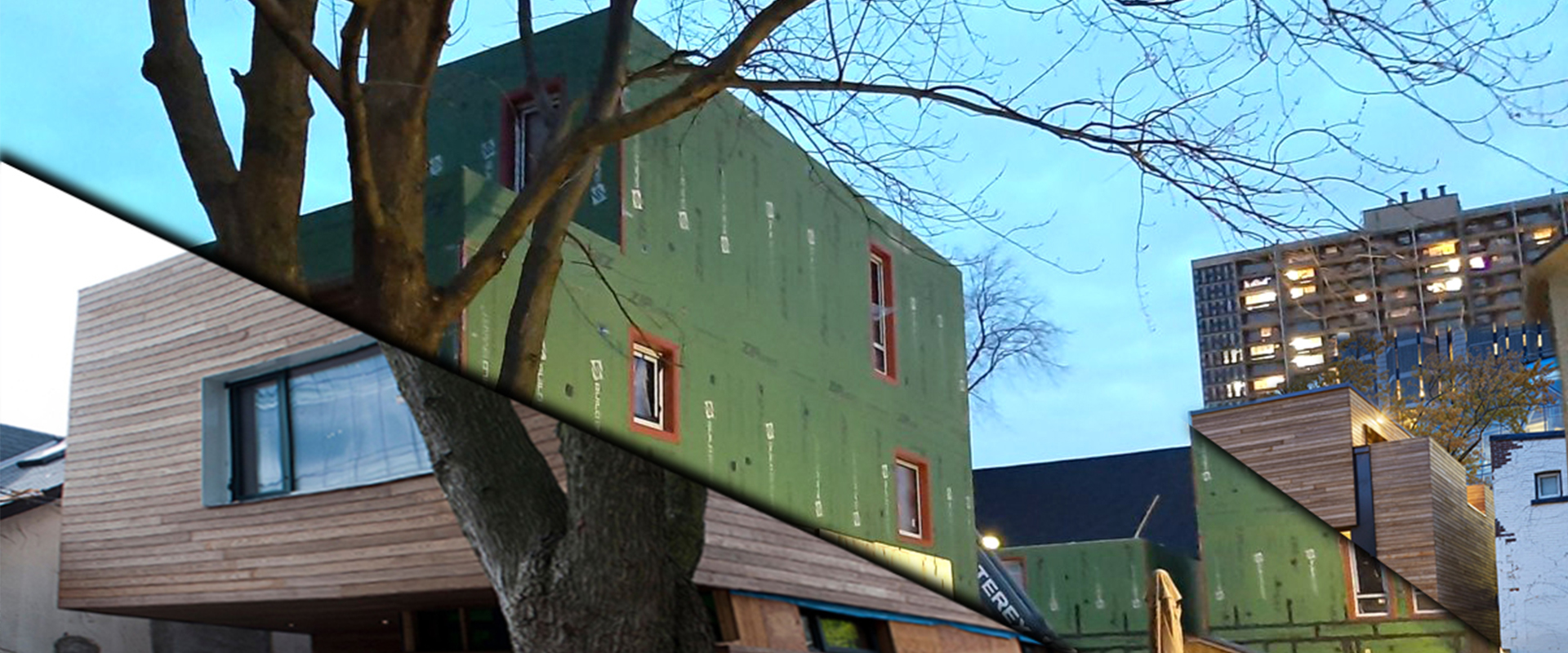
“Beautifully designed and beautifully built”
This laneway housing project, designed by BSN Architects, received a SAB Award for small residential category (2021). Local Impact Design was Passive House Consultant, energy modeler and structural/HVAC engineer. The project is exemplary in a number of ways, proving the concept of pre-fab + Passive House + net zero energy. It also demonstrates that high performance / low impact construction can be less complicated and delivered without a cost premium over traditional construction, helping make Passive House and compact laneway living accessible to wider audiences. The houses are all-electric, operating in concert with passive solar, active rooftop solar PV and passive earth-tube preconditioning to achieve Net Zero energy on an annual basis.
The project includes three new detached residential homes located on adjacent lots at 366/368 Huron St, Toronto. The three houses were conceived as a contemporary intervention sympathetic to the scale, massing, and surrounding site context. The buildings are strategically clustered to create a shared outdoor courtyard space. The mandate of this prototype was to drive a larger initiative for affordable, sustainable infill housing on existing sites within walking distance of the campus, that meets the challenges of 21st century housing – urban infill density that’s low carbon, affordable, and healthy to inhabitants.
Passive House Strategy
Passive House methodology was adopted to optimize both energy and lifecycle cost. Shell consists of R-45 prefabricated wall panels from Build Smart, Thermapan R-54 Structural Insulated Panels (SIPs) for the roof, and Alpen Passive House triple glazed windows (R7) and a shallow super-insulated foundation system (R-24) by Legalett. At its heart, Passive House is an economic solution developed to minimize life-cycle cost and cost of ownership, optimizing return on investment for improving building envelope to reduce heating loads. Basically, the cost premium for added insulation and triple-glazed windows is mostly if not entirely offset by savings from eliminating a furnace and perimeter heating and, in this case the cost of natural gas hookup since the houses are all-electric. Ontario’s electricity grid is 90% GHG-free, so the best way to reduce carbon is to build all electric. But electricity is expensive, so dramatically reducing heating and cooling loads was necessary to ensure that the buildings were cost-effective to operate. Reducing heating and cooling loads to the point where electrical solutions are cost-effective could only be possible using the Passive House envelope-first approach, together with passive strategies like passive solar and earth tube. Of course, the low life cycle cost is where Passive House really shines, with the business case improving as we see carbon pricing and reduced access to affordable fossil fuel. By improving building envelope, Passive House also results in a more comfortable house free of mold.
Prefabricated Passive House Shell
Our decision to utilize prefabricated building panels for the shell was a key strategic decision motivated by several intersecting benefits:
Quality – Pre-fab removes the uncertainty of builder-related quality issues on site because fabrication of the all-critical air, vapour and thermal barriers is done in the factory by trained labour working under controlled environmental conditions. Even the windows were pre-installed in the factory. The wall layers – air, thermal, vapour and weather resistive barriers – are integral to the panel and protected from damage during subsequent fit-out construction. Prefabrication enabled tighter construction tolerances and reduced air leakage. With the shell completed, the first-effort blower-door test was 0.5 air changes per hour (ACH), which beat the Passive House requirement of 0.6 ACH – with no leak chasing required. Because the quality is baked into the panels, site review is reduced.
Schedule – Overall, prefabrication shortened the construction schedule by 2 months, reducing impact to neighbours, including a daycare. Starting with the foundation, the Legalett frost-protected slab-on-grade foundation eliminated the need to dig foundations to below frost level. This was critical to reducing disruption, time and cost plus it eliminated the need for shoring to protect neighbouring buildings. The insulated tray system also enables a single concrete pour versus three pours for a standard foundation (slab, frost-wall and footing). For the prefab walls and roof, standardizing the components and drawing details streamlines design considerably. Fabrication of panelized sections occurs off-site, concurrent with site preparation, thus reducing overall construction time and construction loan financing costs. The tight infill lot had extremely limited laydown area, so panels were trucked to site as needed and erected in place. Site installation takes mere days, allowing us to pick a good weather window for the install.
Cost – Using a factory setting allows a Lean production method, and a pre-fab install minimizes the transport of workers and equipment between job sites. Off-site modular construction can save between 10 and 25 percent in building costs compared to on-site construction. For the University, a big plus was that pricing could be fixed early in the project design phase which helps with budgeting and construction financing.
Operating Energy
The infill home uses only 33% of the total annual electricity that an equivalent house designed to the Ontario Building Code (OBC) would consume. Despite using standard heat recovery ventilators (HRV’s) and electric baseboard heaters (for cost reasons), the Laneway Houses use only half of the annual energy of an equivalent Code-built home. This is due to the passive house shell and the earth tube passive HVAC strategy plus other energy conservation measures including LED lighting and Energy Star appliances.
Designed to achieve net-zero annual energy, the buildings incorporate solar PV panels by Guelph Solar, both on the roofs and south wall of the 3-storey laneway house. Total annual generation for the 18 kW system is estimated to be 712kWh. With a combined projected annual energy use of 19,767kWh, and combined renewable energy generation of 20,075kWh, the prototypes are projected to achieve Net Positive energy over the year.
Projected annual energy for each of the three prototypes is noted in the accompanying chart, which slightly exceeds PH performance standards. This exceedance is due to site specific shading conditions/reduced solar access, and regulatory constraints which limiting glazing facing the southern property line. Future laneway houses located on east-west lanes with improved solar and reduced regulatory constraints should outperform the EUI benchmarking established by these prototypes.
Water Conservation
The project utilises low-flow, WaterSense certified plumbing fixtures throughout and Energy Star rated washing machine and dishwasher. The inline water heaters provide instantaneous hot water and heat recovery is used on the shower drains. This enables a 51% reduction in water used over an OBC design building. 100% of storm water is recharged on site within the courtyard using a French drain system buried below grade.
Materials and Resources
The use of wood and engineered wood products forms part of a sustainability approach based upon the utilization of renewable, carbon sequestering building materials. The houses are clad in thermally treated ash – a product that has become readily available as a result of the environmental impacts caused by the Emerald Ash Borer, an insect that feeds on ash trees. The ash siding has been treated to remove naturally occurring sugars from the wood, which dramatically improves resistance to rot and insect damage, providing the siding with enhanced longevity and low maintenance. The houses are constructed upon a super insulated foam foundation system that utilizes engineered fill and avoids the need for deep concrete foundations, further reducing the carbon footprint of the project and impact to neighbours. In addition to improving the overall sustainability and energy efficiency of the houses, the shell prefabrication approach results in major reductions to on-site construction waste and landfill. Lumber wastage in the factory is less than 5%.
Building Life Cycle Considerations
The environmental impact of buildings begins with material extraction, and continues through fabrication, transportation, construction and operation, before ending with disassembly and disposal. Life Cycle Assessment influences material selection as well as the choice of building systems.
At its heart, Passive House is an economic solution developed to minimize life-cycle cost and cost of ownership, optimizing return on investment for improving building envelope to reduce heating loads. Basically, the cost premium for added insulation and triple-glazed windows is mostly if not entirely offset by savings from eliminating a furnace, perimeter heating, and natural gas/propane hookup. The Passive House envelope-first approach, together with passive strategies like passive solar and earth tube, reduce heating and cooling loads to the point where electrical solutions are cost-effective. The low life cycle cost is where Passive House really shines, with the business case improving as we see carbon pricing and reduced access to affordable fossil fuel.
Education and Information Sharing
The ultimate success of sustainable design will require both a top down and bottom up approach. It will depend on transforming the cultural attitudes among building owners, and disseminating information among professionals to push the envelope of best practice standards. At the same time, public education will raise the awareness and expectations of building occupants and users, and encourage market transformation.
The Huron St Laneway Housing project represents an integrated solution that proves the concept of pre-fab + passive house + Net Zero energy, demonstrating that high performance doesn’t have to be more complicated or expensive than traditional home construction, helping make Passive House accessible to a wider audience

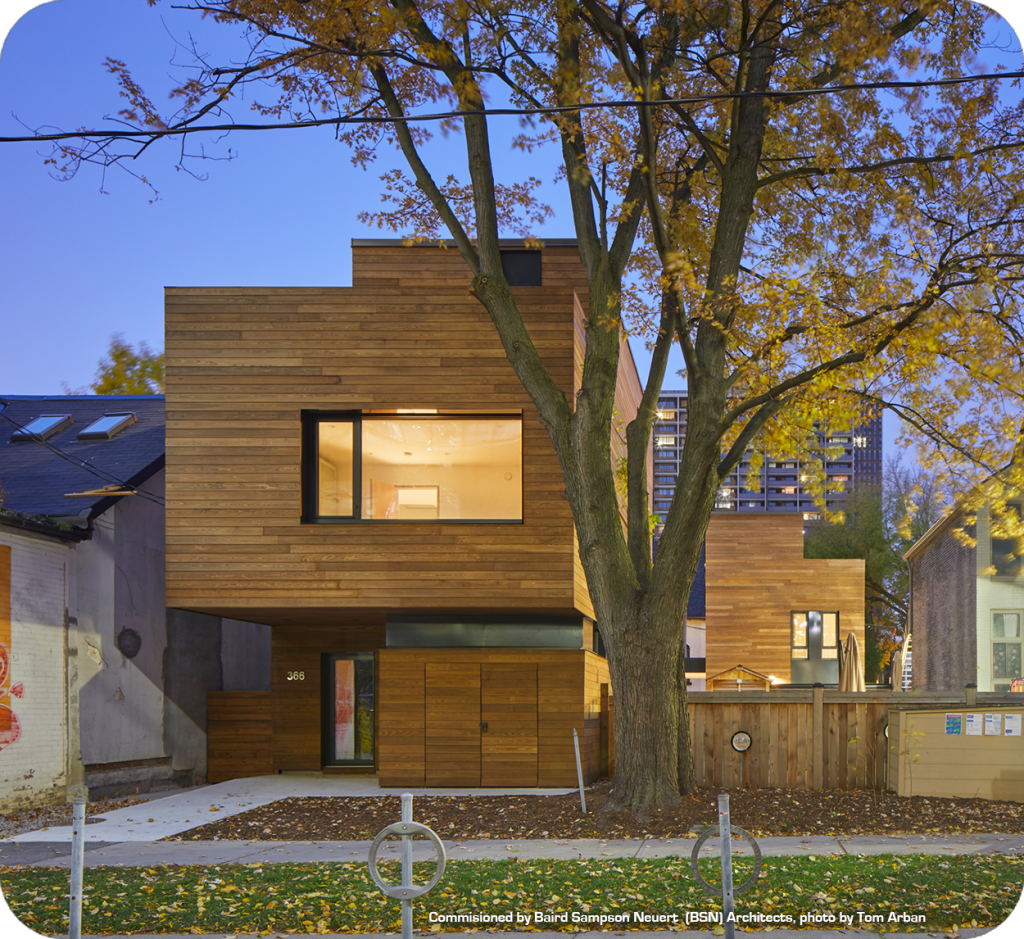
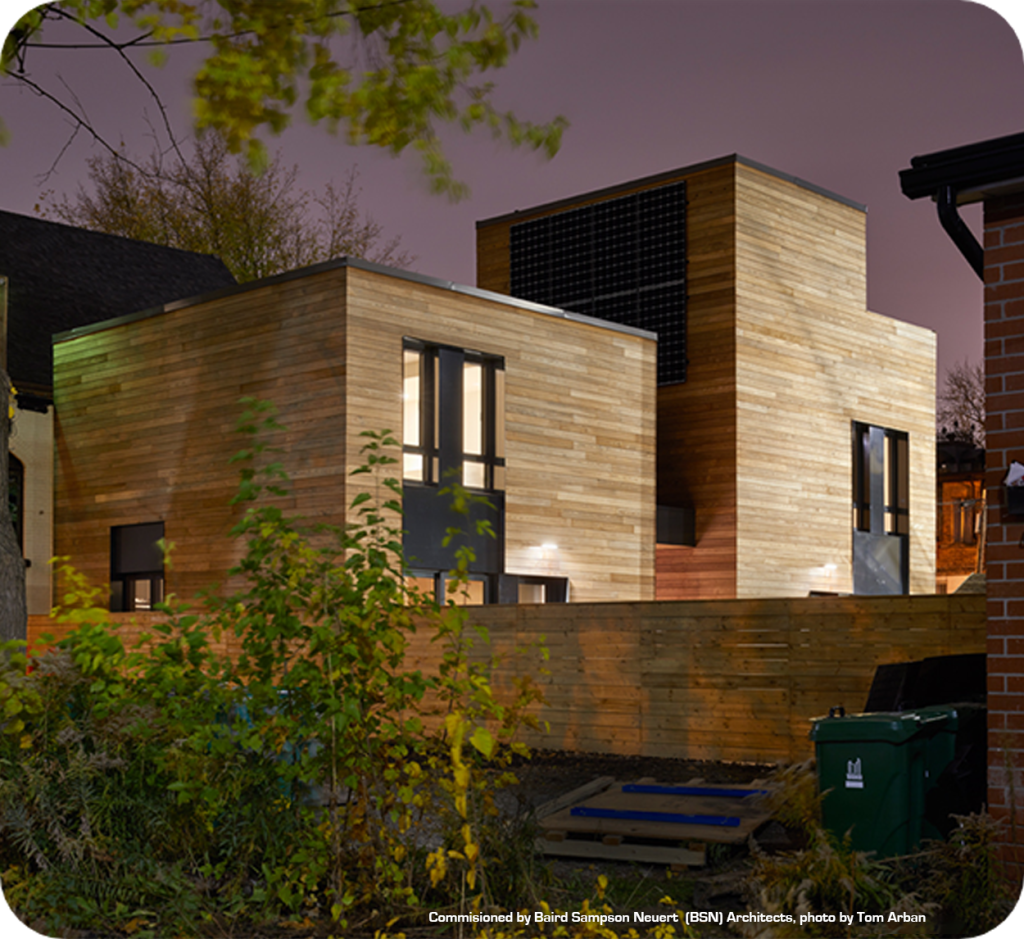
Awards | 2021 Canadian Green Building Awards
Performance Target | Passive House, Zero-Energy, LEED
Cost/Lf | $287/LF
Size | 3 units, 4,500 square feet
Completion Date | 2021
Energy Usage | Annual energy use: 19,767kWh – Renewable Energy Generation: 20,075kWh
Air Tightness | 0.57ACH50
Exterior Walls | Build SMART E-Wall: R-45, 2×4 3 7.5” in Exterior Insulation
Roof Structure | Thermapan R-54 Structural Insulated Panels (SIPs)
Windows | Alpen Passive House triple glazed windows (R7)
Foundation | Legalett shallow super-insulated foundation system (R-24)
Ventilation | Build Equinox CERV2 automated conditioning Energy Recovery ventilation system
Heating & Cooling | Sanden cold climate heat pump
Photovoltaics | Guelph Solar, 18 kW PV system
